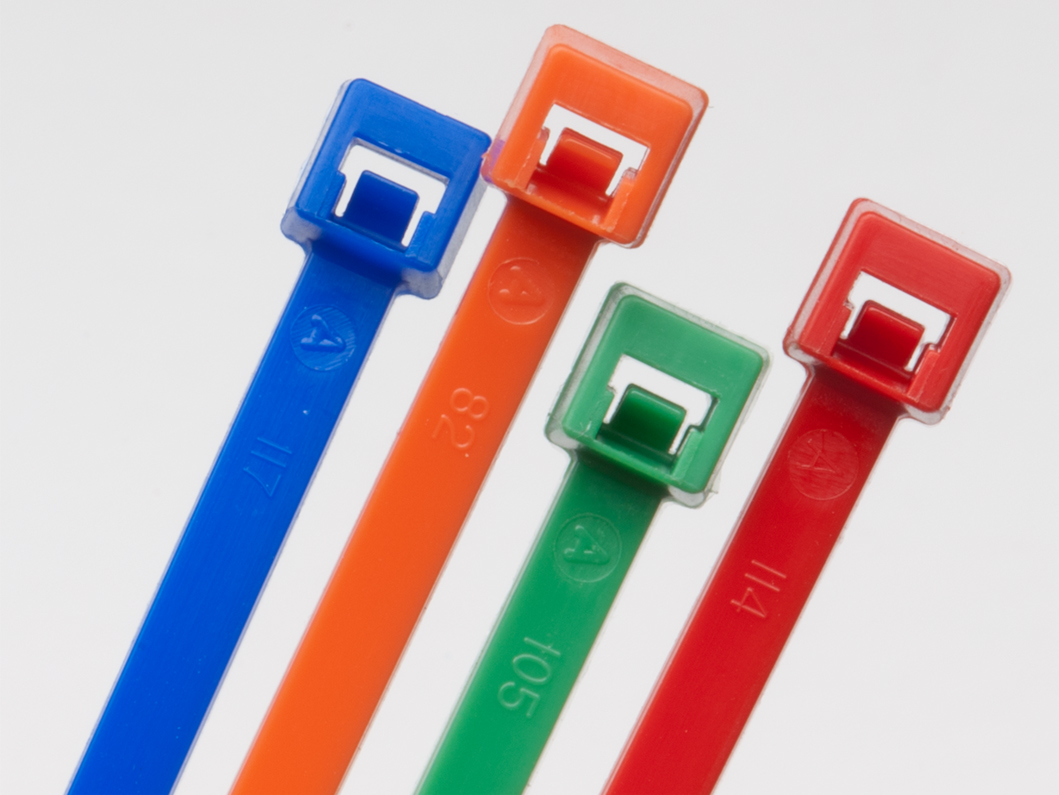
Even though it isn’t as widely used as Nylon 6-6, the semi-crystalline polyamide known as Nylon 12, Polyamide 12 and PA 12, has physical properties that make it an exceptional material for manufacturing many different products. It is used in cable ties, wire insulation, flexible hosing, nozzles, damping cogwheels, flexible cover caps, sheet gaskets, sealing rings, protective coverings, medical catheters and even ski boots.
With a lower concentration of amides (nitrogen-containing organic compounds) than any other commercially available polyamide, Nylon 12’s material characteristics make it beneficial in the following ways:
- • It absorbs very little moisture, which allows components made from Nylon 12 to retain a high degree of dimensional stability, even in environments with fluctuating humidity levels.
- • When temperatures dip below freezing, Nylon 12 still retains excellent impact and non-impact strength.
- • It repels chemicals, including hydraulic fluids, oil, fuels, grease, salt water and solvents.
- • Nylon 12 can withstand cracking under stress, including instances when it encapsulates metal components.
- • It provides superior resistance to abrasion.
- • When it is dry run against steel, polyacetal, polybutylene terephthalate (PBT) and other material, Nylon 12 has a very low coefficient of friction.
- • It dampens noise and vibration.
- • Even when placed under high-frequency cyclical load, Nylon 12 remains incredibly fatigue resistant.
- • It is highly processable.
Below, you’ll find tables listing typical material properties for three commonly used versions of Nylon 12: standard, semi-flexible, and flexible.
STANDARD NYLON 12
PROPERTY | VALUE |
---|---|
Density | 1.01 g/cm² |
Surface Hardness | RR105 |
Tensile Strength | 7251.89 psi (50 MPa) |
Flexural Modulus | 1.4 GPa |
Notched Izod | 0.06 kJ/m |
Elongation at Break | 200% |
Strain at Yield | 6% |
Maximum Operating Temp. | 158°F (70°C) |
Water Absorption | 0.25% |
Oxygen Index | 21% |
UL 94 Flammability Rating | V2 |
Dielectric Strenth | 60 MV/m |
Heat Distortion Temperature @ 0.45 MPa | 302°F (150°C) |
Heat Disortion Temperature @ 1.80 MPa | 131°F (55°C) |
Material Drying | 2 hours @ 194°F (90°C) |
Melting Temperature Range | 374°F - 410°F (190°C - 210°C) |
Mold Shrinkage | 1.5% |
Mold Temperature Range | 104°F - 140°F (40°C - 60°C) |
SEMI-FLEXIBLE NYLON 12
PROPERTY | VALUE |
---|---|
Density | 1.03 g/cm² |
Surface Hardness | RR85 |
Tensile Strength | 4351.13 psi (30 MPa) |
Flexural Modulus | 0.55 GPa |
Notched Izod | 0.07 kJ/m |
Elongation at Break | 300% |
Strain at Yield | 30% |
Maximum Operating Temp. | 158°F (70°C) |
Water Absorption | 0.2% |
Oxygen Index | 21% |
UL 94 Flammability Rating | V2 |
Dielectric Strenth | 55 MV/m |
Heat Distortion Temperature @ 0.45 MPa | 284°F (140°C) |
Heat Disortion Temperature @ 1.80 MPa | 158°F (70°C) |
Material Drying | 2 hours @ 194°F (90°C) |
Melting Temperature Range | 374°F - 392°F (190°C - 200°C) |
Mold Shrinkage | 1.4% |
Mold Temperature Range | 104°F - 140°F (40°C - 60°C) |
FLEXIBLE NYLON 12
PROPERTY | VALUE |
---|---|
Density | 1.03 g/cm² |
Surface Hardness | RR80 |
Tensile Strength | 3625.9 psi (30 MPa) |
Flexural Modulus | 0.4 GPa |
Notched Izod | 0.07 kJ/m |
Elongation at Break | 300% |
Strain at Yield | 37.50% |
Maximum Operating Temp. | 158°F (70°C) |
Water Absorption | 0.2% |
Oxygen Index | 21% |
UL 94 Flammability Rating | V2 |
Dielectric Strenth | 55 MV/m |
Heat Distortion Temperature @ 0.45 MPa | 275°F (135°C) |
Heat Disortion Temperature @ 1.80 MPa | 122°F (50°C) |
Material Drying | 2 hours @ 194°F (90°C) |
Melting Temperature Range | 374°F - 392°F (190°C - 200°C) |
Mold Shrinkage | 1.4% |
Mold Temperature Range | 104°F - 140°F (40°C - 60°C) |